Todays article mostly is on the reverberatory furnace. However, this is the beginning of a small series of articles that are concerned with casting of larger objects: Cannon, bells and statuary art. Only recently my colleagues and I published an article on the written evidence with regards to the casting of the large bronze statues. Or so we thought; the statues from the Hofkirche in Innsbruck were made from brass (Mödlinger, Asmus & Ghiara, 2024).
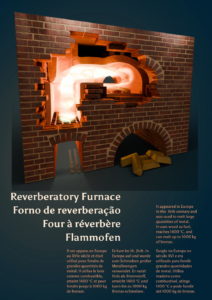
A reverberatory furnace hypothesis based on a 16th description (Asmus, in prep)
The beginning of the 16th century is commonly accepted as the end of the middle ages and the beginning of the modern age. This does also apply to the metallurgical trades, because around the same time the reverberatory furnace makes its appearance in Europe. Seemingly out of nowhere, or at least without any apparent predecessors, the reverberatory furnace manifests itself as fully evolved piece of technology in the metal trades. Leonardo da Vinci and Buonaccorso Ghiberti, nephew of the famous Lorenzo Ghiberti left us with sketches of these furnaces. Artists and scholars like Vannoccio Biringuccio (1540) or Benvenuto Cellini (1974, 2005) left us with treatises, where they provide insights into the design and use of these furnaces.
This type of furnace appears more or less suddenly at the beginning of the modern era. There are nor real preceding furnace designs from the middle ages in Europe, so there is a possibility that this concept arrived in Europe as a new concept. The reverberatory furnaces are one key component in the Industrial Revolution (Bulstrode 2023) as puddling furnaces for the making of steel, from scrap iron and also from raw cast iron.
A reverberatory furnace for Vianden
The reverberatory furnace for Vianden is a new reconstruction based on a 16th century treatise of the founding of cannon (Asmus, in prep). The experiment follows the instruction closely and will use it to cast a cannon, based on one cannon found at castle Brandenbourg, Luxemburg. It is one of the two cannon made by Casper Bux from Vianden in the 16th century.
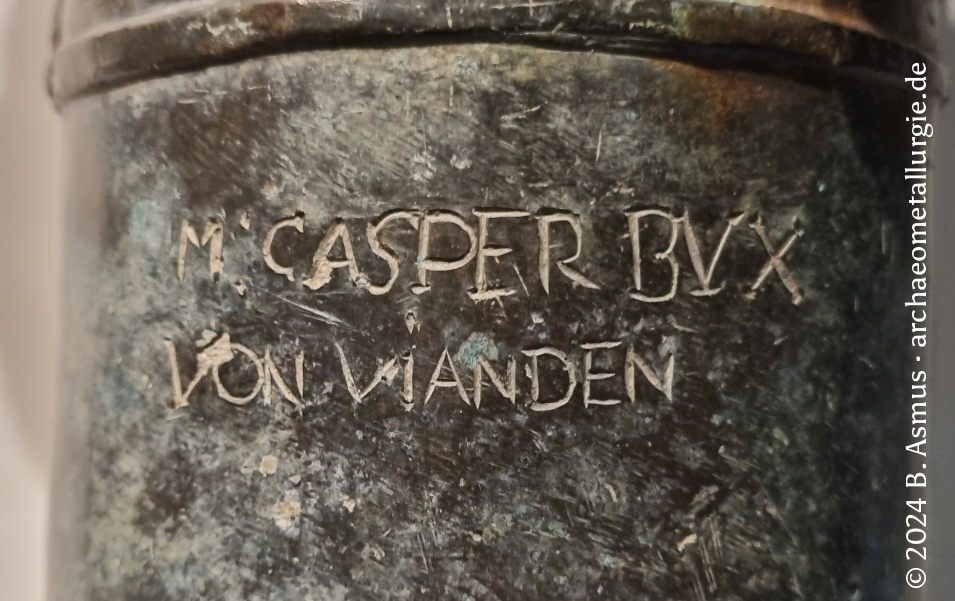
The signature of Casper Bux von Vianden.
The cannon mould will also be made experimentally following a variety of 16th century at the Castle Vianden. The whole process can be seen live at the castle.
A reverberatory furnace not only for cannon
The Vianden reverberatory furnace is far more than only for cannon casting. With the very same furnace we can cast bells by or the cast of statuary art. As a fully trained bronze caster I do have strong interest also in bronze sculpture, and from the above mentioned Cellini treatise we know that his Perseus with Medusa was made by such with the reverberatory furnace.
To this end I hope that we can use the Vianden reverberatory many times for the purposes of contributing towards the understanding the intricacies of Renaissance bronze casting and beyond.
References
Brepohl, E. (ed.) (2005) Benvenuto Cellini. Traktate über die Goldschmiedekunst und die Bildhauerei. Böhlau Verlag.
Benvenuto Cellini (1974) Abhandlungen über die Goldschmiedekunst und die Bildhauerei. Translated by Max Fröhlich. Basel.
Mödlinger, M., Asmus, B. and Ghiara, G. (2024) ‘The “Schwarze Mander” of the Court Church in Innsbruck, Austria: Manufacture and Production of Monumental Brass Statues in the Renaissance’,
International Journal of Metalcasting [Preprint]. Available at:
https://doi.org/10.1007/s40962-024-01299-4.