Jan
22
2014
Bastian Asmus

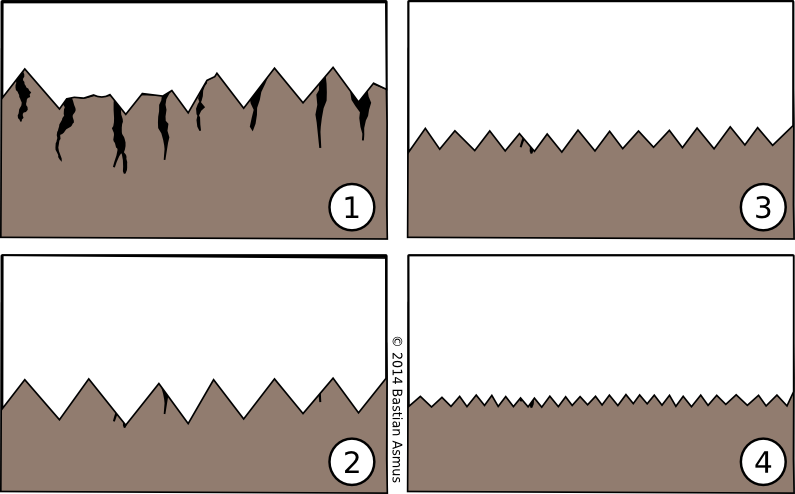
Highly magnified schematic view of a cross section through a sample during the grinding process. Grinding serves two purposes, first to remove micro-shattering caused by cutting (1 and 2), second to prepare the surface for polishing (3 and 4). With consecutive smaller grits you have to remove the scratches left by the previous grit.
Hello to part four of the slag microscopy series. After mounting, it is about time to start sample grinding to prepare the section for polishing.
For this we need:
- a sample polisher/grinder
- abrasive discs
- optional: stereo-microscope to inspect grinding progress
- optional: a marking gauge
Polished section needs to flat. Bottom and top surfaces of the section have to be plane-parallel. A good polish is only achievable if the surface has undergone adequate preparation. This is done by grinding on a horizontal water lubricated abrasive disc. Flatness is usually achieved with abrasives bonded on paper, in synthetic materials or in metal. Continue reading
1 comment | tags: How to | posted in Archaeometallurgy, Lab work, Microscopy, reflected light microscopy, slag
Jan
15
2014
Bastian Asmus


Image 1: The series on slag microscopy you will tell you about how to prepare, describe and interpret polished sections of slag samples. After that you to get hold of a microscope and invest time…
This is the first article of a series on slag microscopy. Excuse me, on what?
Yes you did read correctly: I said slag microscopy. –
This will be a series of articles thought as an introduction to the most noble and useful art of slag microscopy, the equipment needed to do slag microscopy and what slag microscopy is all about. Today’s topic is sample preparation! Slag microscopy is a small but fun part of one the most fascinating disciplines of archaeology: archaeometallurgy (: and it is very useful for us archaeometallurgists, too.
Why? Because slag tells us a lot about the processes and products of which slag is a by-product. In order to be able to tell what slag tells us we need to have a look at it through the microscope. We have to prepare a polished section and will describe the microscopical appearance of the sample under the polarising reflected light microscope.
1 comment | tags: How to | posted in Archaeometallurgy, comparative collection, Lab work, Microscopy, Science, slag
Jun
30
2013
Bastian Asmus
[tab: Description]
Bastian Asmus 2012:
Medieval Copper Smelting in the Harz Mountains, Germany (= Montanregion Harz, Bd 10 [Hg. Christoph Bartels, Karl Heinrich Kaufhold und Rainer Slotta]), Bochum (Veröffentlichungen aus dem Deutschen Bergbau-Museum Bochum Nr 191), 2012, ISBN 13: 978-3-937203-63-8
395 pages, english, colour, Appendix for microscopic identification (reflected polarising lihjt microscopy) of slag phases, metal phases, ore minerals and their analysis by SEM-EDS, WDX and EPMA-WDS as well as XRF for bulk chemical characterisation.
44,- Euro
Medieval copper from the Harz
The work deals with the evaluation of a high medieval smelting site in the Harz, near the UNESCO World Heritage sites Rammelsberg and Goslar. With more than 1000 m2 excavated it is to date the most extensive archaeometallurgical investigation of a smelting site in medieval central Europe. It is a site where the polymetallic Rammelsberg ore was smelted to produce copper, lead and silver. The site can be considered as a typical example of a high medieval smelting site in the Harz. Particular emphasis was placed on an interdisciplinary approach which drew upon historical, archaeological and material scientific sources.
[tab: abstract]
Abstract
The Rammelsberg deposit in the Harz mountains in Germany is among the largest metal deposits in the world and has been in continuous use for more than a millennium. There is much controversy as to the nature of the metals produced and the processes involved from the ores of this deposit. This thesis deals with the largest and most accurately excavated smelting site of the high medieval period in the Harz mountains called Huneberg and may be regarded as typical for region and period.
Traditionally historians connect the Rammelsberg with silver production, the mining historians, however point out that the deposit is too poor in silver and that copper was produced in the high medieval period. Modern economical literature classifies the Ram- melsberg as a lead-zinc deposit.
To contribute towards the understanding of these questions an archaeometric study of archaeometallurgic waste- and byproducts, such as slag, furnace lining, furnace wall, litharge and spilled metal drops was undertaken. It builds the base of the interpretation of the metallurgical activities that have taken place at the Huneberg and is contrasted with previous studies. It is suggested that copper, lead and silver in form of argentiferous lead were produced on site, using a complex multi-step process, taking full advantage of the numerous structural features of the site, e.g. the three furnaces present on the site. Successive smelting episodes produced black copper of increasing purity as well as a rather rich argentiferous lead. Because the site is similar to may other sites it is further suggested the mode of metal production at the Huneberg followed a more or less stringent set of recipes and traditions. The mass of 1600 kg slag recovered from the site suggest a copper production of some 600 kg or less, depending on the ore quality. Lead is thought to have been produced in similar quantities, which in turn would mean that the site produced also 1.4 kg of silver during its operation.
[tab: Order info]
Order
44,- Euro plus P&P
Online shop of the German Mining Museum
[tab:END]
no comments | posted in Archaeometallurgy, Science